DEVELOPMENT OF STEEL CHEMICAL COMPOSITION AND HEAT TREATMENT REGIME OF RAILWAY WHEELS FOR OPERATION IN LIGHT BRAKING CONDITIONS UNDER HIGH AXLE LOADS
DOI:
https://doi.org/10.30838/J.PMHTM.2413.240422.9.837Keywords:
railway wheels; chemical composition; decay kinetics; heat treatment; stiffnessAbstract
The development of new wear-resistant materials has a pivotal role in solving the durability problem of railway wheels. The adoption of appropriate chemical compositions of steel and proper heat treatment regimes aimed at developing specific structural conditions for manufacturing railway wheels will increase wear-resistance, contact fatigue and brittle fracture resistance. Purpose of research. The research suggests methods for the development of steel chemical composition and rational parameters for the class D railway wheels heat treatment (light braking conditions and high loads on axle with increased wear resistance), which will ensure realization of the AAR M-107/M-208 standard requirements. Methodology. In the laboratory, experimental meltings with different content of alloying elements are done. A complex setting consisting of closed type melting unit ICEF-0.01 and high-frequency current source HFTG-20-22 is used. Laboratory steels are subjected to hot plastic deformation and heat treatment in regimes closing to the industrial ones in the manufacture of a railway wheel. The kinetics of austenite decay during continuous cooling at different rates with dilatometric method is investigated. Mechanical properties are determined with standard methods. Results. Experimental steel is made and investigated. Railway wheels from experimental steel of the recommended chemical composition are manufactured. Scientific novelty. The regularities of the austenite decay kinetics at continuous cooling of experimental composition steel: 0.68 % C, 0.49 % Si; 0.7 % Mn; 0.77 % Cr;
0.22 % Ni; 0.069 % Mo; 0.087 % V for class D railway wheels, designed for operation in light braking conditions under high axle loads according to requirements of AAR M-107/M-208 standard are determined. The regularities of change in the austenite decay mechanism in a wide range of cooling rates are determined. Up to 1 °C/s, the austenite decay proceeds with the formation of a completely pearlitic structure. At a cooling rate of 2 °C/s, the structure is 15 % perlite, 25 % bainite, the rest is martensite and residual austenite. At cooling rates ≥ 5 °С/s the structure of martensite and residual austenite is formed. Practical significance. The recommendations for steel chemical composition and thermal strengthening technology of wheels to obtaining a high complex of class D railway wheels mechanical properties according to requirements of AAR M-107/M-208 standard are developed.
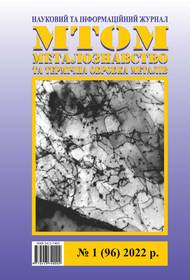
Downloads
Published
Issue
Section
License
Authors that are published in this journal agree to follow the conditions:
Authors reserve the right to the authorship of his work and cede the right to the journal of first publication of this work on conditions of the license under the Creative Commons Attribution License, which allows others to distribute it freely with the obligatory reference to the author of the original work and the first publication of the work in this journal.