Optimization of tin and aluminum content in tin bronze according to mechanical properties indicators
DOI:
https://doi.org/10.30838/J.PMHTM.2413.050722.41.858Keywords:
tin bronzes, aluminum bronzes, mechanical and technological properties, alloying elements, optimization, simplex-planning methodAbstract
Problem statement. New compositions of foundry bronzes in which the best levels of properties inherent in both tin and aluminum bronzes are combined need to be developed. Purpose of research. Regularities between mechanical properties indicators and alloying components content in bronze of Cu−Sn−Al system with tin and aluminum content up to 6 % each are obtained. Methodology. Alloys for investigation was prepared by technical purity primary charge materials melting in induction crucible furnace using graphite crucible and charcoal as a coating material. Investigated alloys mechanical properties was calculated based on tests results of corresponding samples during their static elongation and impact bending at room temperature according to actual standards. Alloys chemical composition control was carried out on precision analyzer EXPERT 4L on samples cut from cross-shaped samples. Investigated multicomponent system response surfaces plotting was performed by H. Scheffe simplex-planning method with models of fourth and third degree. Results and discussion. According to Cu−Sn−Al alloys research results, functional dependences between mechanical properties vs. Sn and Al content from 1 to 6 % by weight of each are determined. This makes it possible to predict the level of mechanical properties according to chemical composition of such bronze during casting. Conclusions. It was found that within tin and aluminum content in investigated limits the best combination of mechanical properties has bronze BrO3A3 with content of Sn = (3…4) % and Al (3…4) %. Bronze BrO3A3 has higher (including plastic) mechanical properties values compared to the properties of tin bronzes, which are most often used in industry. This gives the reason to recommend such bronze for shaped castings and friction bearings manufacturing.
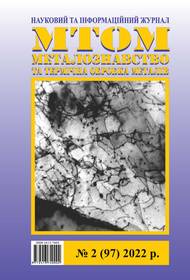
Downloads
Published
Issue
Section
License
Authors that are published in this journal agree to follow the conditions:
Authors reserve the right to the authorship of his work and cede the right to the journal of first publication of this work on conditions of the license under the Creative Commons Attribution License, which allows others to distribute it freely with the obligatory reference to the author of the original work and the first publication of the work in this journal.